This article is Part 2 of 2 in a series. In case you missed Part 1, you can find it here. Image above: Makerspace SLUB. Credit: Wikipedia
Makerspaces
Makerspaces are places where people share tools and knowledge to build whatever they want. Developed out of MIT’s “Fab Lab” concept, hundreds have sprouted up all over the country in the last 5-10 years. They function like a community center, with tools – or in the case of Hatch (or HATCH), a “tool collection” and free classroom. Now, full disclosure: I volunteer with HATCH, and I’m paid to teach classes there.
Hatch started in a mall that the Watertown public had commissioned be rebuilt out of an old Federal armory. As of this writing (3/27/2017), HATCH is still there – though the section it resides in will be destroyed and Hatch will need to move to somewhere else.
Still, being in a mall, across from a big open Innovation Space which is like a less cool Innovation Center, has given HATCH a unique perspective in America – as of this writing, there are no other makerspaces in malls. That and the fact that “WFPL” on that logo means “Watertown Free Public Library”, means that the Watertown Library, and thus, the People of Watertown’s tax dollars, are going directly into community education programs.
But from what I’ve seen, this place has been a boon to the local area. People come in and are genuinely curious – something different than all the shops and places to spend money. They can create, and not just consume. I’ve taught everyone from 10 year olds to 65 year olds how to 3D model and 3D print and in my experience, people are excited to learn to do real things, things that are considered “cool” by modern standards. These are folks that would not traditionally go to a library, attend a trade school, or take a shop class (if they still had them). But because Hatch exists, they are given that chance.
In this way, Makerspaces act as an educational branch of government, and can augment it in ways that are real and tangible. If we want to talk about bringing back manufacturing to America, then we have to talk about how to update the ways people learn those skills. The people that were put out of work 20 years ago by outsourcing, etc. are not going to know how to just jump back into the workforce. Manufacturing isn’t the same anymore – and we have to invest in ways to teach people these new skills so that they can get those decent, livable wages and jobs. Makerspaces already bring life to local communities by acting as a fun place to gather and rally around – but they also teach useful skills, and even act as startup incubators, providing people with the tools and knowledge to launch local businesses and improve the areas they’re located in. They’re like a shop class, community rec center, library, and startup incubator – all rolled into one. They can be public or private, though public will have greater reach due to it being free to taxpayers. Makerspaces are the best avenue for leading the charge in re-educating America’s population to become producers, and not just consumers.
Microfactories
Microfactories were first proposed by the Japanese Mechanical Engineering Laboratory in 1990 (Source: Wiki). I’ll quote the general idea behind them:
“The microfactory’s main advantages are to save great amount of resources like space, energy, materials and time.”
Again, I gave a talk on this stuff – so I’m going to try to refrain from repeating everything. But if you’ve ever heard of a job shop you have the basis for a microfactory. For those who don’t know; a job shop is a shop that focuses on specialized portions of the production process. For example; one job shop might exclusively cut, bend and weld metal. Larger companies, like John Deere, contract out sections of their product manufacturing schedule to these shops, so that the parent company doesn’t have to invest in the often expensive equipment and processes. Job shops also can do small one-off orders for individual customers as well.
Now, a microfactory takes this general idea and both expands and refines it. The biggest idea behind a microfactory is “just-in-time manufacturing”. Using digitally-driven processes microfactories focus on producing just as much as they need, when the customer buys the order. The ideal would be to drive down waste and increase profit, by not having a stack of inventory sitting around and creating pressure on the sales funnel.
Microfactories are also different from job shops in that they focus on end-to-end production with a variety of processes and fewer people, higher automation. The idea here is that A) a microfactory will be able to take your startup idea from nothing all the way to those first 1,000 or 10,000 units and B) the focus is on building as directly from the CAD file as possible.This is done with as little human interaction as can be had (Digital Direct Manufacturing, or DDM, is the term for this in industry). A microfactory is supposed to be able to provide everything you’d need to create a product of n-complexity on demand. Perfect for startups looking to bridge production before going full-scale, or existing companies looking for a quick way to validate products and expand their offerings for their clients.
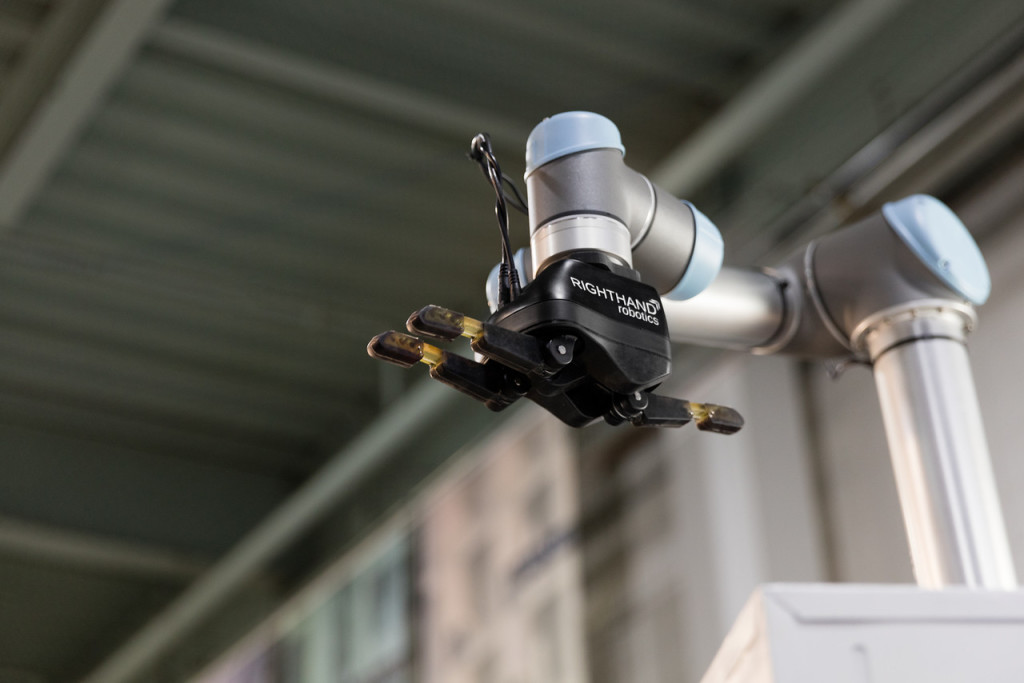
Digital Direct Manufacturing (DDM) is the idea that what is in CAD is what comes out of the machine as the final product – i.e. there is zero to very little human interaction in the creation of the product. The epitome of DDM is the 3D printer: hit “print”, out comes your final product. Motominded used this principle to great effect when it started: with a bank of 3D printers, the owner was able to go from an idea to a store selling hardware products in just 3 days.
The antithesis of DDM is having factory workers figure out from a plan drawing how something needs to be made. There is very little computerized manufacturing and a lot of production time is spent on manual welding, jig setup, bending, etc. DDM is going to be one of the core tenants in the manufacturing pipeline of tomorrow.
Sustainability
Before we get into “The Future of Production” (I just heard a gong in the distance) let’s talk about Sustainability. Let’s talk about what it really means, because you know what? This idea came out when I was still in college (heck, they even built a center for it), and 5 years later I have yet to see people use it well in advertising or popular culture. Everyone says “oh it’s sustainable to use wood instead of plastic” or something like that, and while they might be technically right, I doubt they know why. Most people take “sustainability” to be another word for “green” or “ecologically friendly.” Let’s really talk about this.
First of all, anything can be sustainable, because sustainable intrinsically reflects a period of time. I can sustain a running pace for about 30 seconds, and then I’m gasping for air. It didn’t last for a long time, but for 30 seconds I output maximum effort. That is what sustainability is really about.
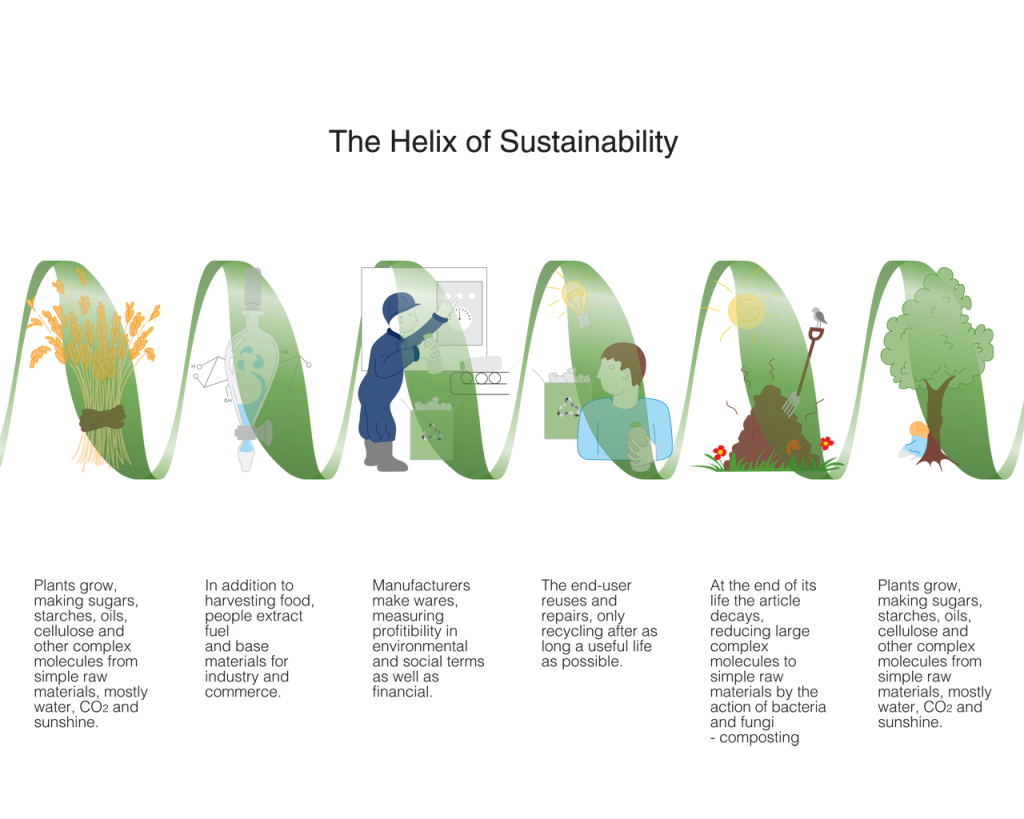
So when we talk about our manufacturing processes, and we talk about how “sustainable” they are, we need to look at the entire life-cycle of the product. One of the key reasons that plastic is less sustainable than wood is because wood can be renewed but it also goes away. It’s hard to sustain product output when you’re buried in trash. On a longer timescale, the energy expenditure required to manufacture and refine wood is much lower than plastic – which means that at a given rate of production output, you can output the same amount of wooden products for a longer period of time given the same assumed maximum energy capacity of the planet/process/factory.
For example; if it takes 20 energy units to produce 1 kg of plastic in one hour and you have 100 energy units total, then you can produce 5 kg of plastic in 5 hours. If it took 10 energy units to produce 1 kg of wood in one hour, and you have 100 energy units total, you could sustain wood production for 10 hours and still produce the same amount of wood as you did plastic.
Now if we’re talking global sustainability, then we have to also factor in the stress of production at speed. If you produced the plastic at a slower rate, than you would have less plastic at any given time, but you would be able to sustain your production for a longer period of time.
Currently, we think about manufacturing as an all-out race to produce as much stuff as can be consumed and “sustainability” as a way of making it “Earth-friendly.” While neither of these items are particularly wrong, the real way they interact is based on a time scale. It’s about measuring the total energy cost of the product over its lifetime: from concept to creation to death of the product. Anything less is doing a disservice to the concept.
The Future of Production
Now that we’ve gotten that out of the way, let’s talk about The Future of Production (bong…bong….) Like we’ve already talked about, DDM is definitely the way forward: companies want to streamline their process as much as possible, and anything that links the engineer’s software to the manufacturing floor will drastically speed up time. Expect to see a lot more investment in digital manufacturing technologies, and companies holding to old-school manufacturing principles will either find their available audience shrink, or they will need to continue finding cheap labor in order to stay competitive.
Factories will be more and more automated. A good rule of thumb is that if you are making lots of copies of something, pretty much every part of it can be automated somehow. So once again: forget about those assembly line jobs you used to see in old footage America. Even China is moving to automation at this point, and they have a larger wealth of cheap labor than the USA ever will have again. That being said, there are a lot of opportunities for versatile people with engineering degrees, so if you want to work in a factory, study up and get high-tech, because they’ll need CNC programmers (seriously, just look on Craigslist and you’ll usually find a bunch), structural testers, factory automation experts, and more.
Cool, so what about the rest of us that don’t have/want an engineering degree? What follows is my ideas, and I present them with the caveat that all of this is innately unpredictable and anyone who tells you that “This Will Definitely Happen” is probably not being quite honest with themselves or you. Even what I said before about factories is suspect, though I’m pulling from the last several years of progress to make that prediction. What follows is what I think will happen after the inflection point – where robots, climate change, and societal upheaval meet.
I believe that eventually, these societal, economic, and climatological pressures will force local areas in the future to become more self-reliant. As we transition into a more automated future and continue the stratification of society into “haves” and “have nots,” we will see more demand for skills that allow people to repair their broken items in order to save money and to preserve functionality. We might move away from the consume-dispose economy towards a consume-repair-pass on world. We can’t have more automation and keep money the same way it’s been since before robots were invented: eventually capital will own all the cash, and labor will not be able to buy anything. So I think we’ll end up with a few solutions, but in the end overall we’ll see an upwards demand for design and manufacturing education as the value of the average person’s paycheck stays static and they need to fix things or design new objects to solve their problems.
That being said, I don’t think everyone will rush out to learn CAD, and stick with it long enough to become an expert. I think we’ll end up seeing more small manufacturing shops (microfactories or makerspaces) crop up to serve local communities and help them produce for their needs. As long as our current economic model holds out, these spaces will play second fiddle to mass produced, cheap objects. But at this point that staying power really is in question: there are a lot of deep-seated assumptions about capital and labor that are being thrown into question in our new world.
However, if we have an explosion of individual value, say, minimum basic income or some other incentive to allow people to spend more money and buy more things, I still think we’ll continue the trend towards design and manufacturing education as a means to mass customization.
At this point, we’ve had years of exposure to products specializing in “making us more us”, so I think in the beginning a lot of this knowledge will be trapped within organizations that had it to begin with. They will use it to sell products and customized solutions for individuals in relatively low volumes – but again, if we have that value explosion, people will be willing and able to pay more for those items.
So really either way we’ll end up with more people making more things: either because the traditional supply chain has been disrupted and they need to fill their needs, or because the traditional economic model has been disrupted and they have more income to spend on bespoke solutions for their lives.
I think that, ecologically, the preference of younger generations to spend money on things that are labeled “sustainable” or “green” will push us more and more towards that in the larger marketplace: witness Tesla. That being said, we might not actually reap the benefits of “sustainability” until we come to grips that it doesn’t just mean “making things out of wood instead of plastic” and it really requires a plan for the birth, life, and death of every product we make. It’s very difficult to get anybody who owns a business to consider how to make arrangements for the orderly demise of their product right from the very start: too many people it’s frightening and they’d rather not think about it. So I don’t really know where that will end up, but I hope that we come out with a standardized energy value system that will help product designers make better decisions about their products and material choices.
One last note. It’s possible that with the trend towards faster delivery times, next day or same delivery, etc., a microfactory could stand to benefit. For example, imagine a factory for the East Coast could produce products and stock them nearby, then deliver them directly to local consumers. For certain products, same day delivery could come from the factory that produces the part, rather than from just a warehouse. In general, I don’t think that our increasingly on-demand culture will be at odds with the movement towards localized manufacturing. Consider that a microfactory can make mass-customized parts more easily than a traditional factory, then one an see
Conclusion
At the end of the day, there is going to be more change in the next 5-10 years of manufacturing than there was in the past 100. I definitely do see a trend towards localized manufacturing because it allows people to launch products more cheaply and quickly than ever before. I also see a trend towards non-standard “manufacturing” training in Makerspaces and the like because it’s needed, and because “shop class” comes with an ugly stigma that students aren’t “smart enough” to learn from books, and adults need a place to go to further their skills as well. I think that’s actually probably the largest change in all of this: educating and growing our adult population’s capabilities after they leave their traditional schooling. By teaching our population about what goes into making things, they can make better choices about the products they do buy. With this knowledge, we can hopefully move towards a more locally responsive, sustainable future.